Benefits of MBJ in Metallic Parts Design — Aerospace Engineering
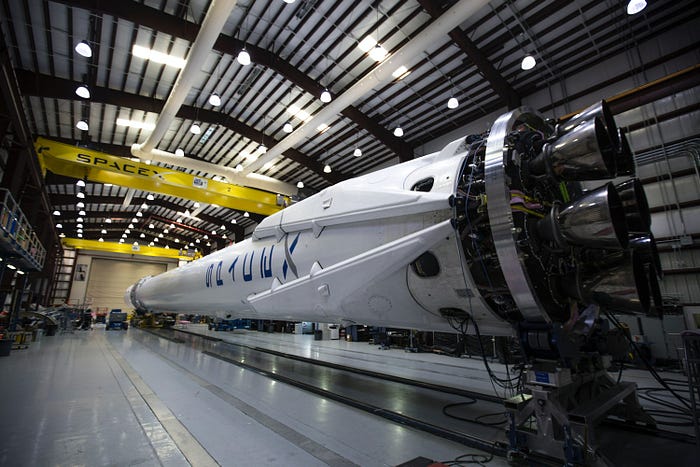
John Wathen IV was an award-winning track athlete and the varsity soccer team captain at Pleasant Valley High School in Brodheadsville, Pennsylvania. After graduating in 2013, John Moss Wathen IV enrolled at Pennsylvania State University, where he received his BS in aerospace engineering in 2017. While attending Penn State, he took courses covering aerospace analysis and aircraft design.
Within the aerospace business, 3D metal printing technologies like binder jetting have established a firm presence. Metal binder jetting is a method of additive manufacturing in which a liquid binding agent is selectively deposited onto a thin layer of metal by an industrial printhead to create high-value components and tools. Utilizing a map from a digital design file, the procedure is repeated in layers until the design is completed.
Metal binder jetting offers various benefits over traditional powder bed fusion procedures, including the ability to print huge quantities of components with minimum spacing and the elimination of support structures. It has the potential to replace low-volume, high-cost metal injection molding in a wide range of applications, including automotive and aerospace parts, as well as medical applications. Because of the high resolution achievable, it may also be possible to cut the cost and lead time for complicated and lightweight metallic parts like turbine wheels and gears.